raku fired pottery
Raku fired piggy-bank
Raku-ware is pottery that has been glazed and fired in a very special and dynamic way.
The pieces are heated in the small, propane powered Raku kiln until the glazes become molten and shiny, around 1000°C/1800°F. At this top temperature, the potter carefully removes the pieces from the kiln with metal tongs and places them on beds of shredded paper and/or sawdust.
As the combustibles ignite, the flames are starved of oxygen by quickly covering the whole thing with a metal bin, causing the flames within to “steal” oxygen from the glazes as they try to keep burning. The flames change the chemical makeup of the glazes and in so doing effect their colours.
In addition, this “post firing reduction” technique generates a lot of carbon which gets driven into any unglazed parts of the pottery, including the unique patterns of crazing that have occurred in the glazes due to the rapid cooling of the pieces. A black, crackled finish and flashes of metallic lustre are distinctive features of this kind of work.
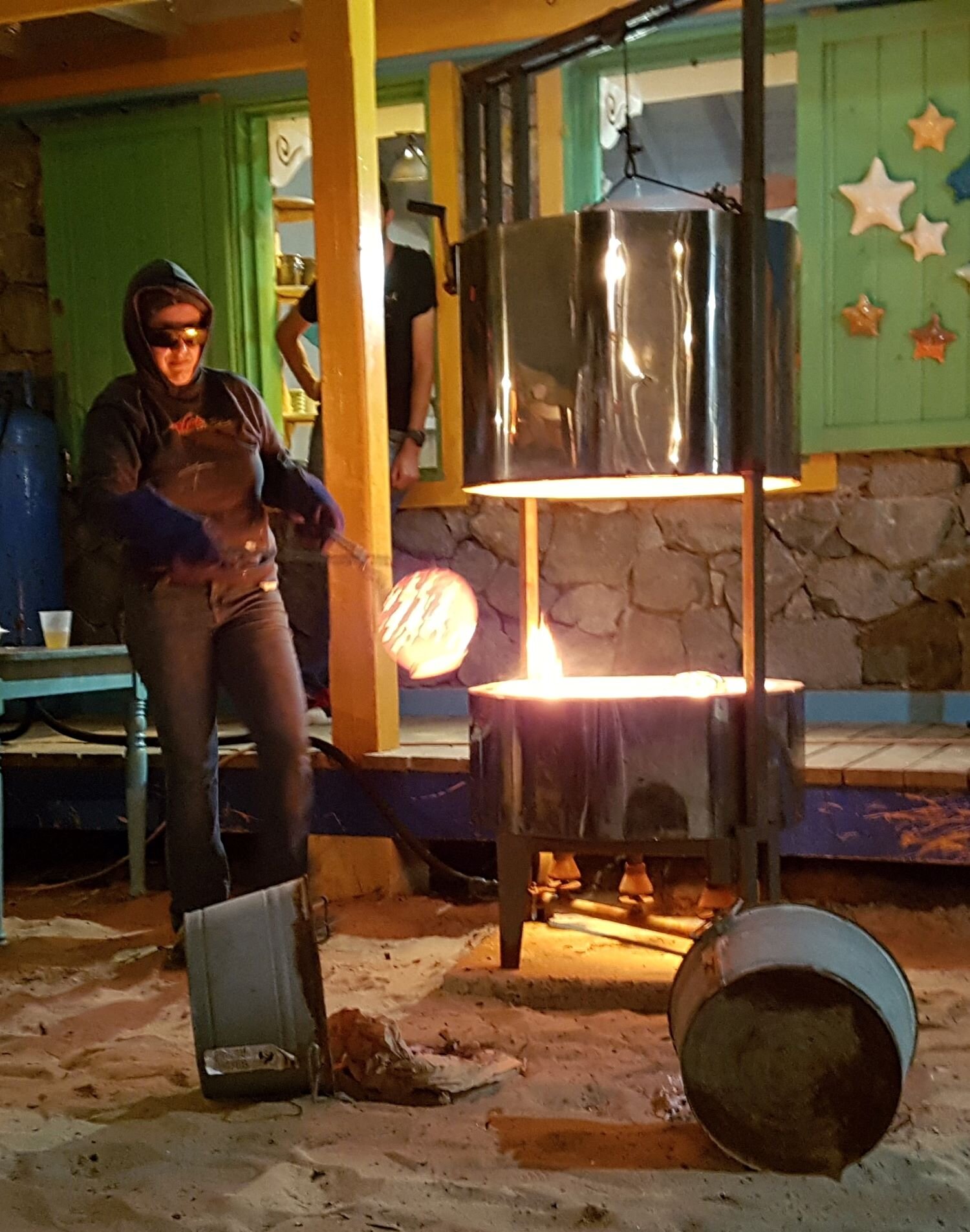
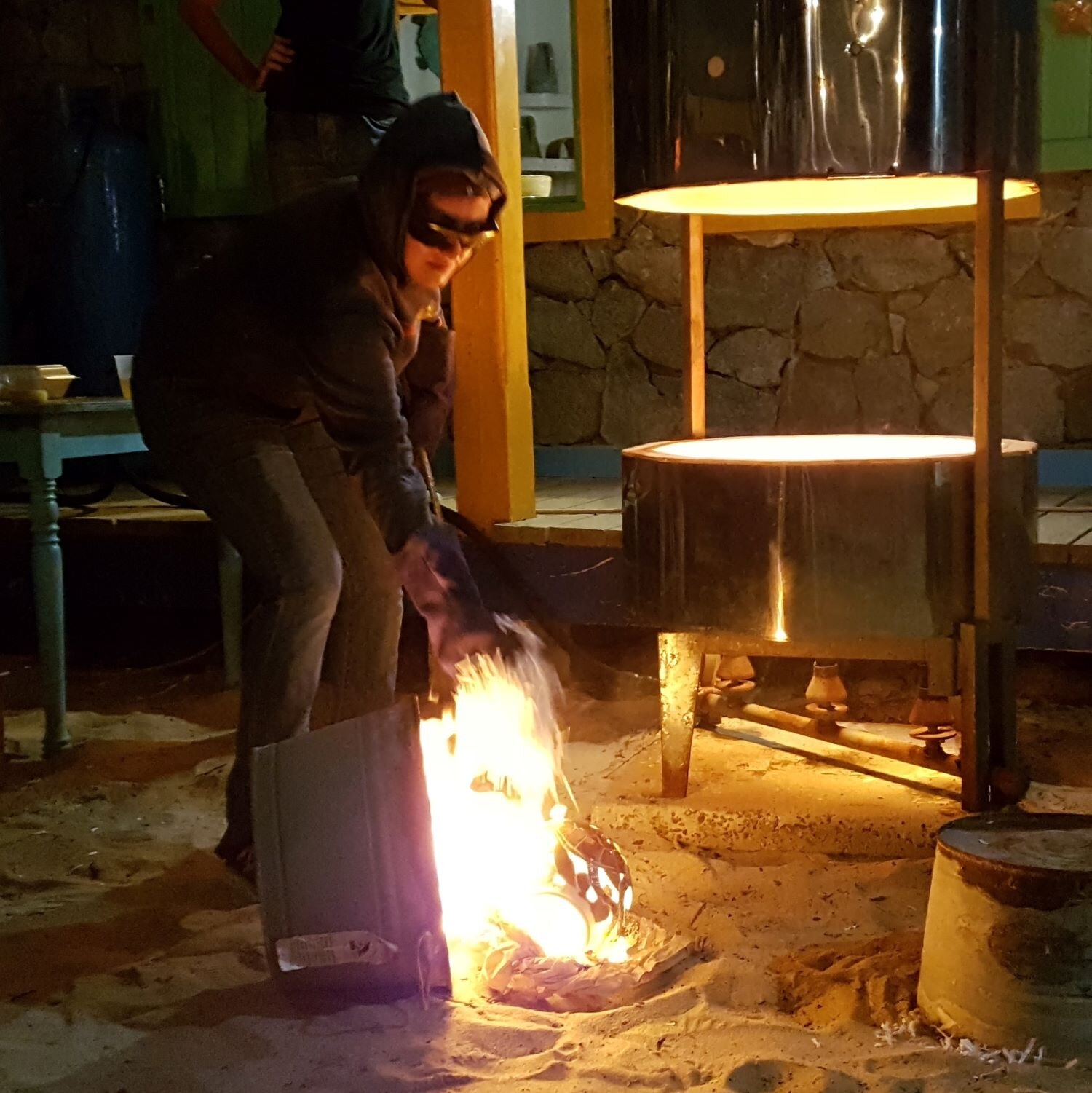

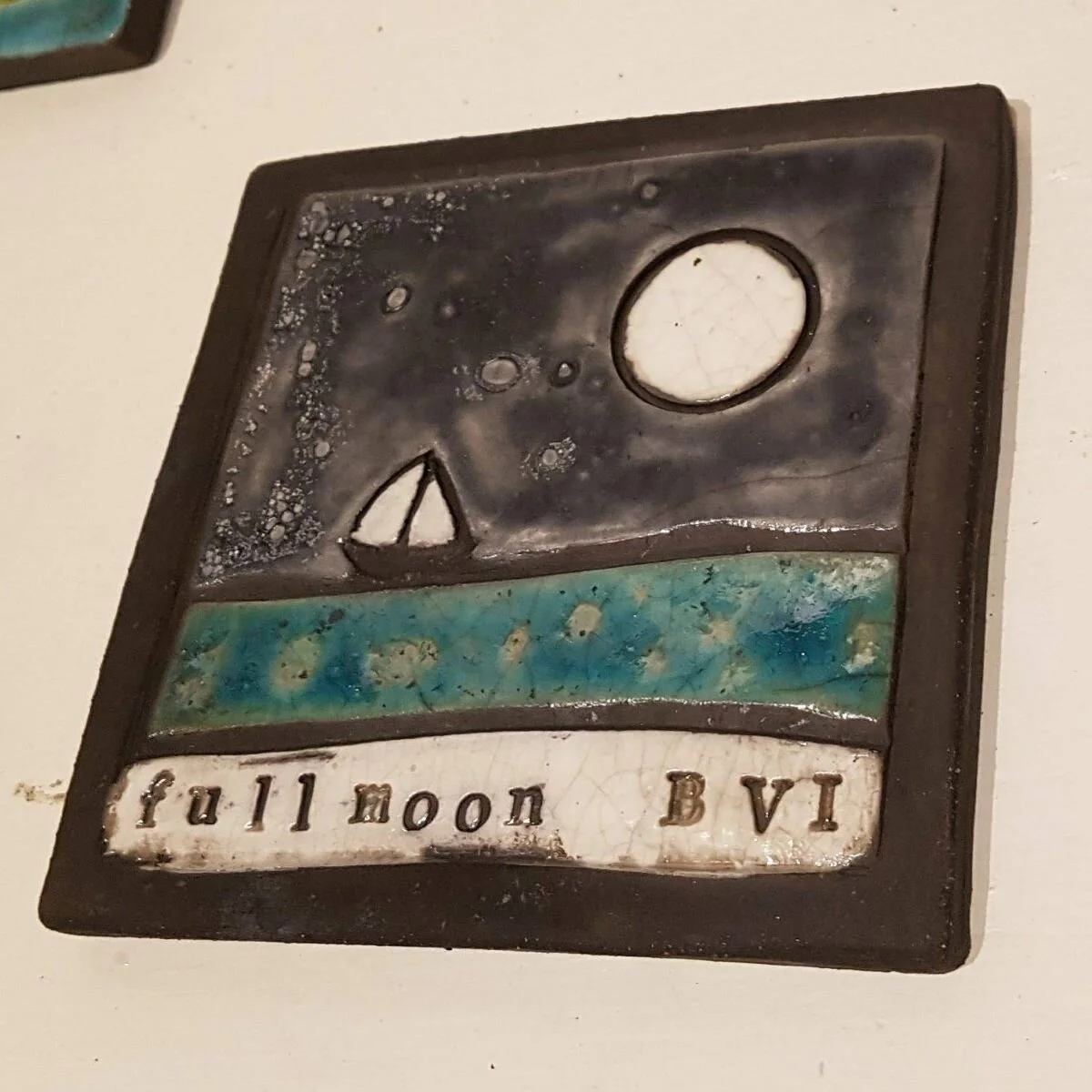
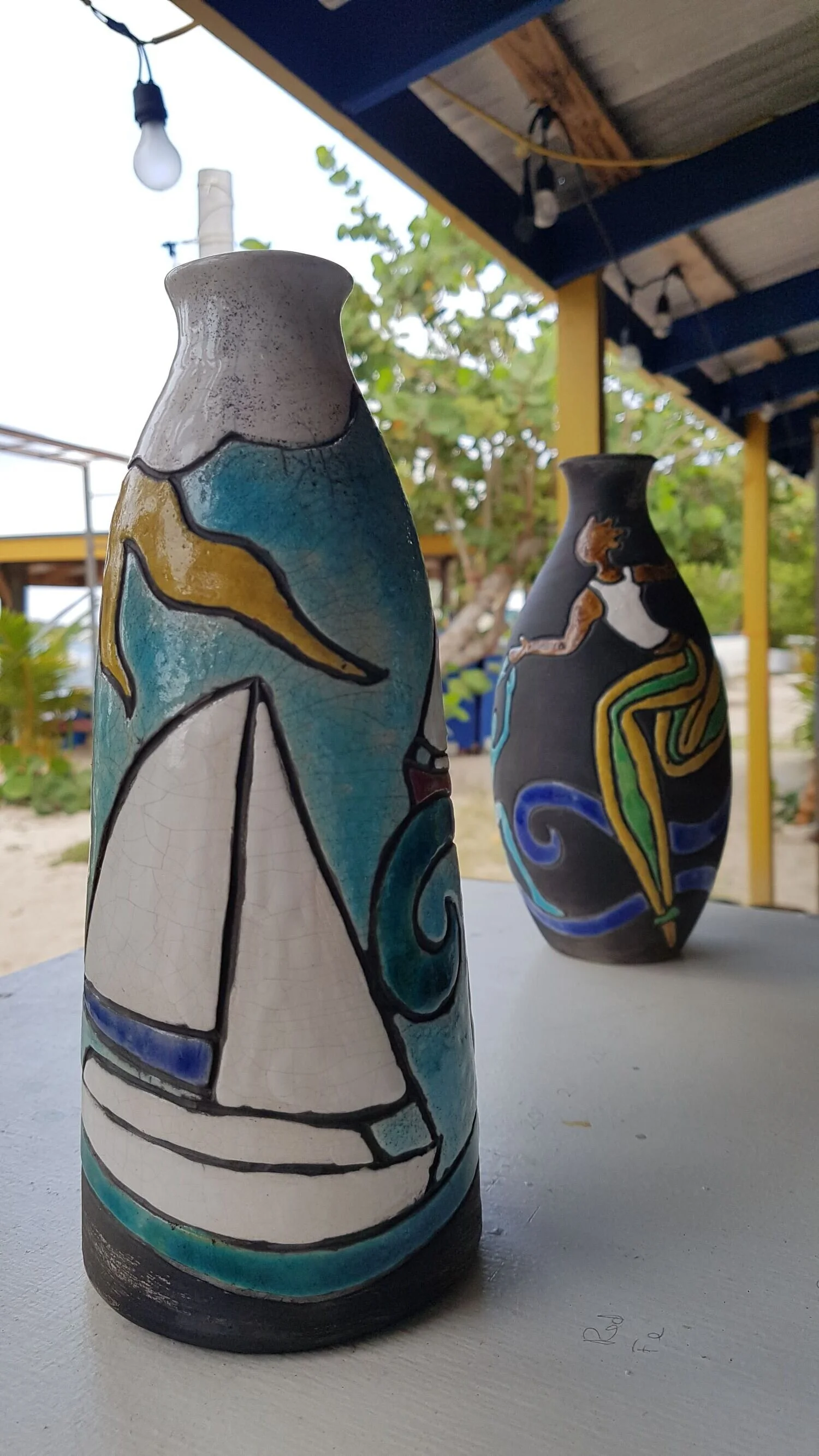
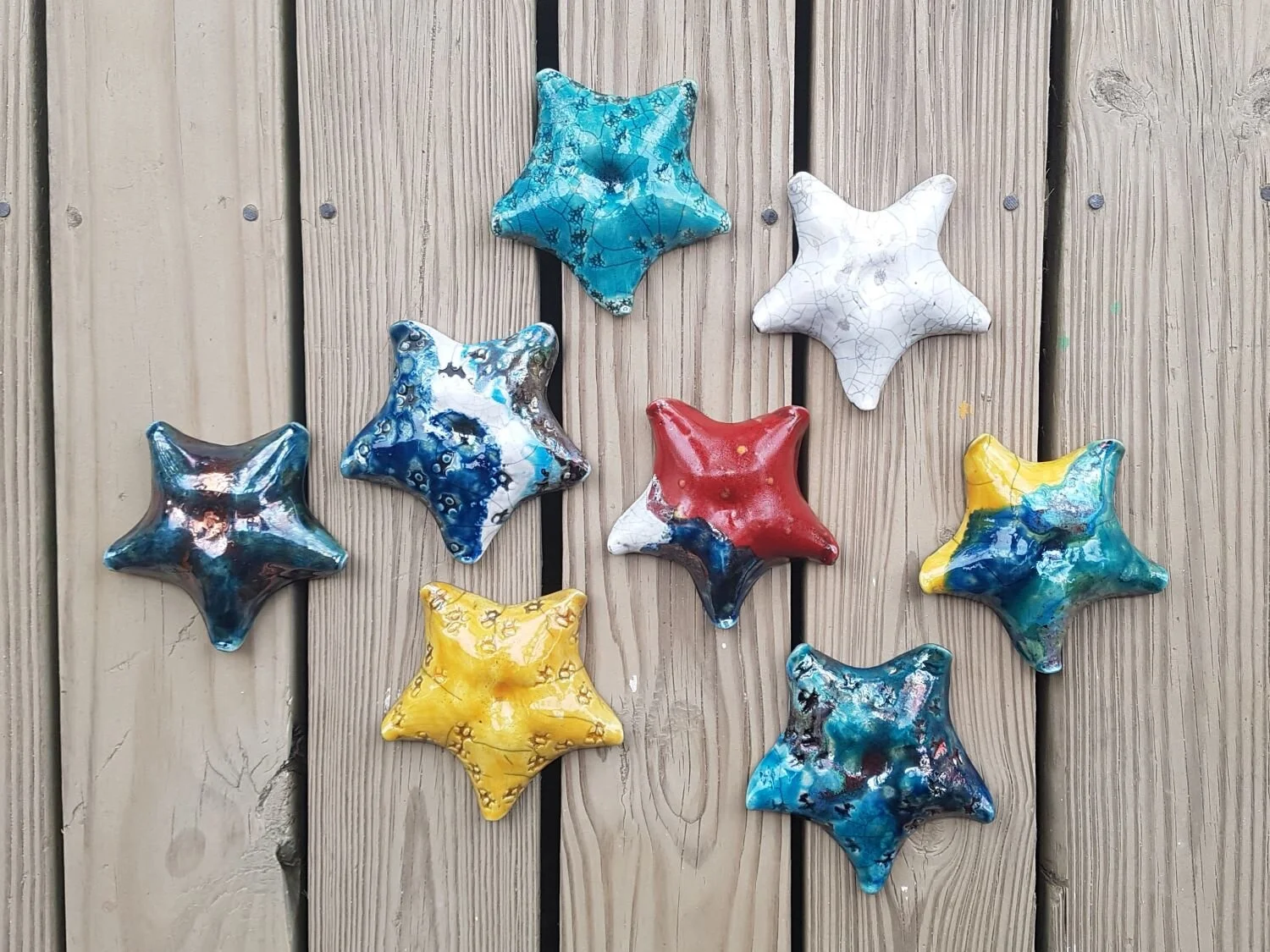
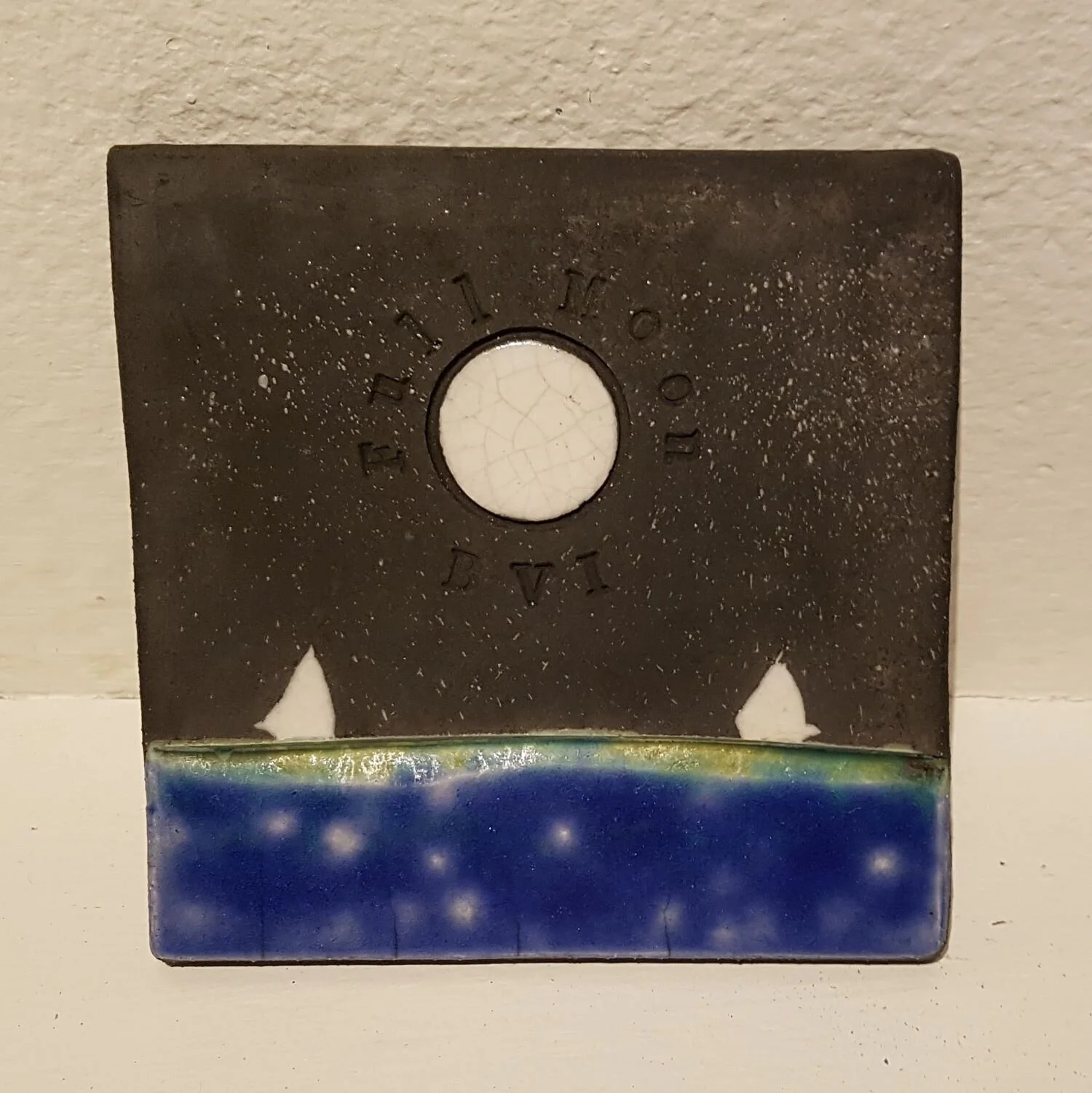

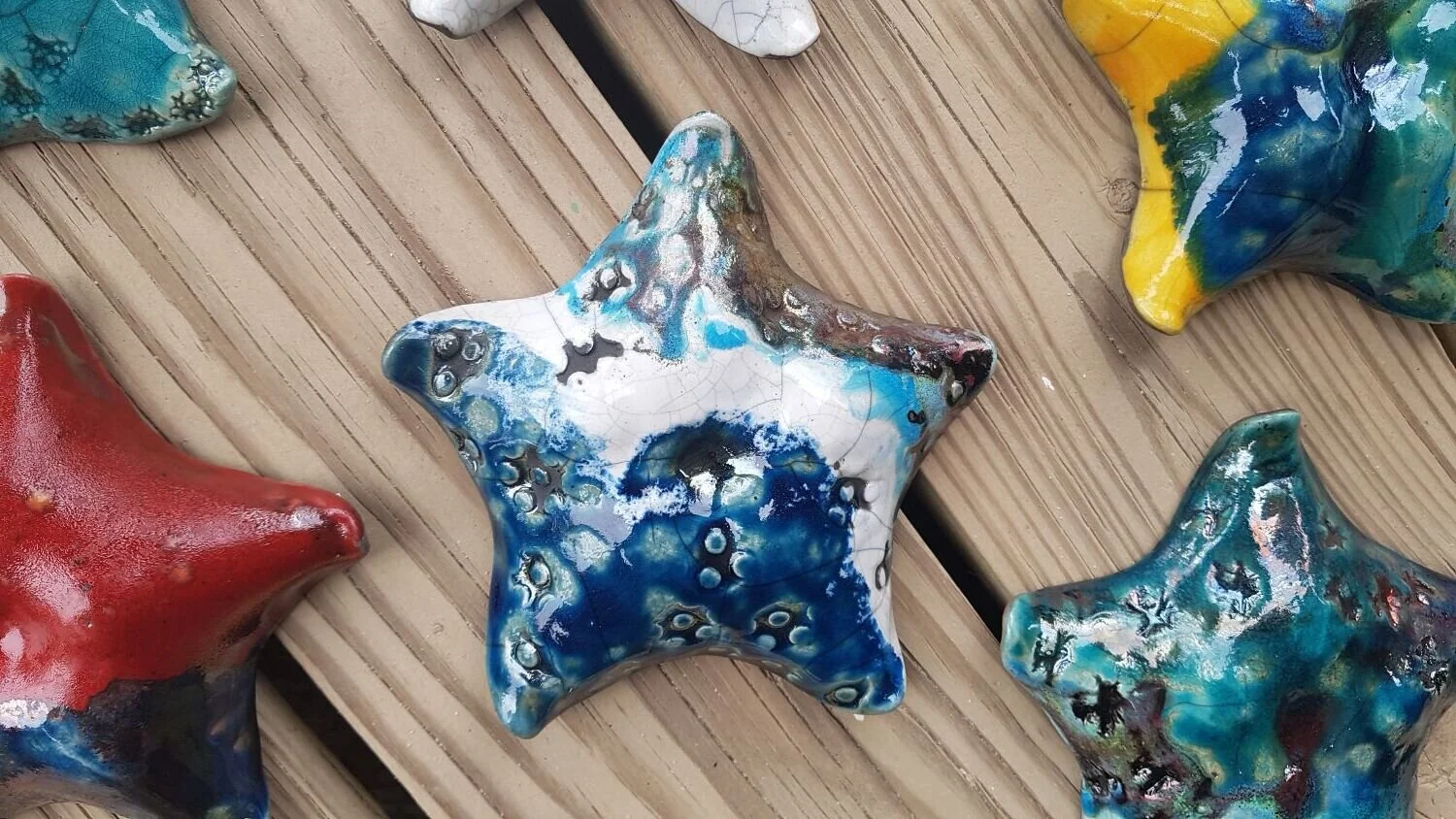